Squeezing Out More Test Coverage: Bridging the Gap Between Boundary Scan and Functional Test
Home / eResources / Squeezing Out More Test Coverage: Bridging the Gap Between Boundary Scan and Functional Test
In todayโs electronics market, the speed and effectiveness of product testing have a significant impact on a productโs overall quality, cost, and time-to-market. All printed circuit board (PCB) manufacturers and test engineers would like to have 100% test coverage of their PCBs, but is this level of test coverage achievable? And if so, at what cost? In the manufacturing test environment, time is money, therefore, manufacturers must make decisions on how much of each they are willing to invest to ensure a quality product.
Boundary scan test, one of the software driven NBT methodologies, has increased in popularity across the PCB test industry. Boundary scan instrumentation within semiconductor devices is used to verify register operation and perform PCB structural testing. As boundary scan technology has matured, it is now used for device configuration and programming along with device functional testing.
Boundary scan can test and validate a broad range of device types on PCBs, however, there are device types that may be excluded from testing due to complex testing algorithms. Consequently, PCB coverage gaps could exist with some devices going untested. To bridge the test coverage gap, end users develop custom scripts to access these devices to apply functional test algorithms via the boundary scan infrastructure. ScanWorks users can bridge the coverage gap between boundary scan and functional test via its Component action. This action allows for testing of non-boundary scan devices, such as analog to digital converters (ADCs), digital to analog converters (DACs), Ethernet PHYs, LED, switches, clocks, and other non-boundary scan devices through the PCBs boundary scan infrastructure.
Key Points:
- Coverage Assessment Methodology
- Achieving Optimum Test Coverage
- iNEMI PCOLA/SOQ/FAM Framework
- Bridging the Gap with the Component Action
- Component Action Facts
- LED Verification
- Connector Verification
- Clock Verification
- ADC with Temperature Measure
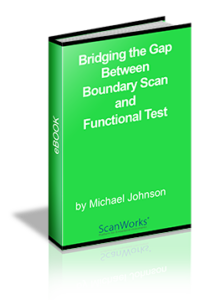